A substantial number of Indian industrial warehouses and manufacturers use a large number of pallets as a one-time purchase asset that helps them manage and move the inventories in house. These warehouses also use wood and plastic pallets and then scrap them after which a third party either dumps or burns or recycles it to the extent it is possible with additional processing cost to be borne by the exporter or the recipient. Recycling for these materials is hardly likely the case as the quality of wood and plastic used is not recyclable after using this as a heavy grade industrial pallet. It is destined to either end up in dumping grounds or water bodies or burned to add to the green emissions, making it unsustainable and inefficient for a large scale of industries. Such has been the scenario until recent times. Imagine, globally there are 4 billion pallets in use currently.
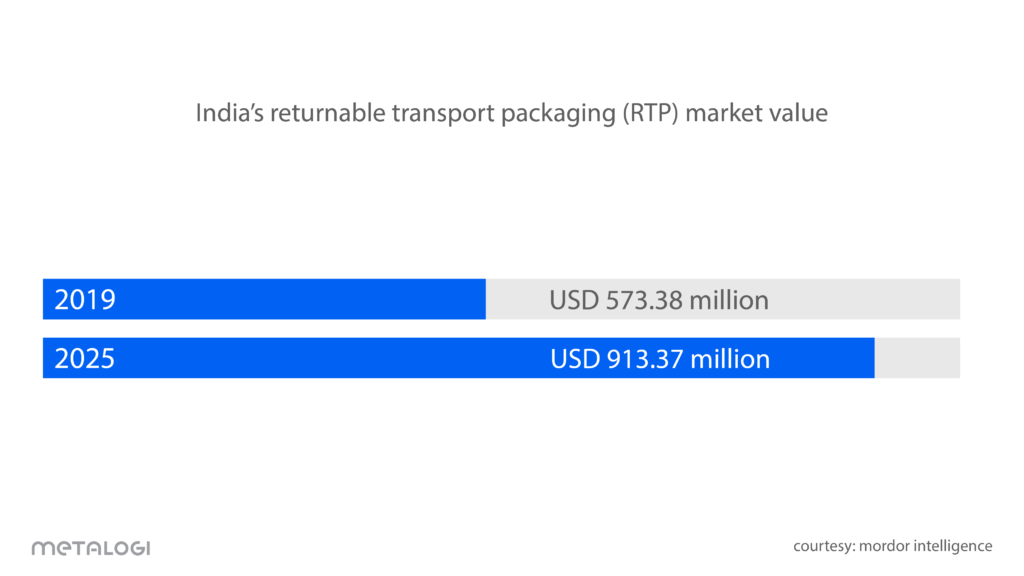
The India returnable transport packaging (RTP) market was valued at USD 573.38 million in 2019, and it is expected to reach a value of USD 913.37 million by 2025 registering a CAGR of 7.9% over the forecast period 2020-2025 (courtesy: Mordor intelligence), which quantifies how much waste is produced each year with conventional use of plastic and wood having its fair share according to this data. Out of these production numbers, a major percentage (approx. 55-65%) is dumped onto grounds and water bodies which creates environmental pollution which accounts to the pollution created by the industrial community even before the product ends up in the hands of the end customers which is another pain point. Only if we could change this scenario we could save this cost and pollution at a large scale at the industrial end itself. We can make a huge difference to the green goals we have as a community of responsible business owners if we seek a smart solution.
Much to the relief, there is a solution industries can adopt which could be a great boon to the environment and helps to lower the cost of ownership of industrial packaging and pallets. Let’s know-how.
metcrate and metcase by metalogi have been developed as an engineered pallet which solves many logistic challenges, thereby making a great add-on to your logistic handling assets for all kinds of warehouses and exports. The benefits are multifold, the main ones to discuss here are the cost reduction by being recyclable and hence earns scrap value.
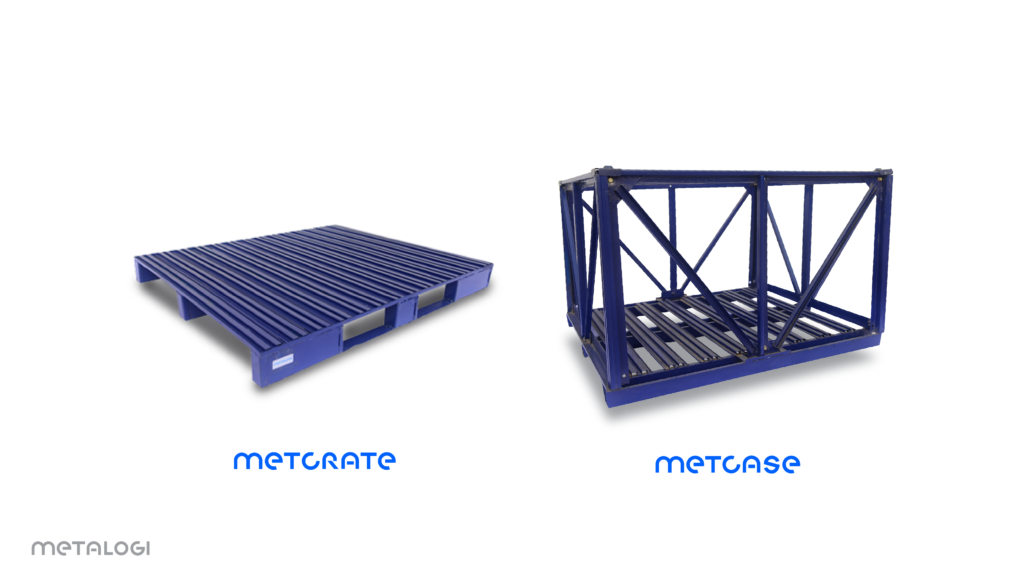
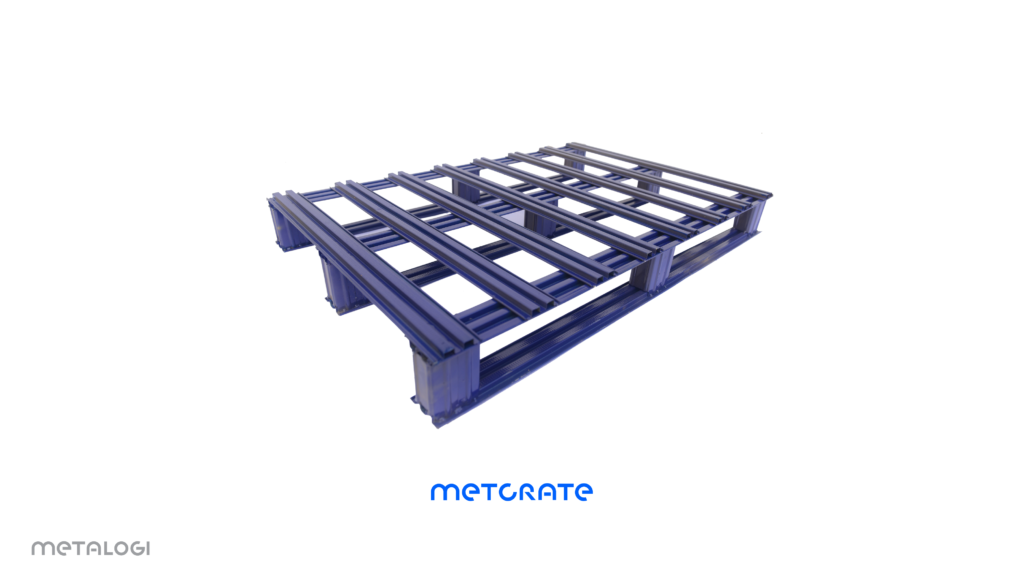
These metal engineered pallets are totally recyclable and totally harmless when recycling without using a high amount of chemicals and energy, it is returned back to the smelting industry and is recycled to be reused with no degradation of environment or quality of the metal. This makes the engineered pallets more user friendly and more cost-effective decreasing the overall cost of ownership by getting returns on the overall buying cost. 30 per cent of the actual cost of pallet gets returned to the buyer after the ‘scrap cost earned’ when the pallet reaches the end of life.
This should be an instant decision for many export manufacturers, who are supplying to the EU and developed nations where this is catching up fast. With this scenario changing drastically across the globe where green emission norms are observed stringently, bans and specific regulations(like IPSM 15 guidelines) have been imposed in Australia, Americas, EU, Canada and African nations when accepting plastic and wood pallets with exported goods. Adoption rates for use inside an industrial warehouse are also changing rapidly with a better cost of ownership that makes exceptional business sense for the warehouse and export-led businesses.
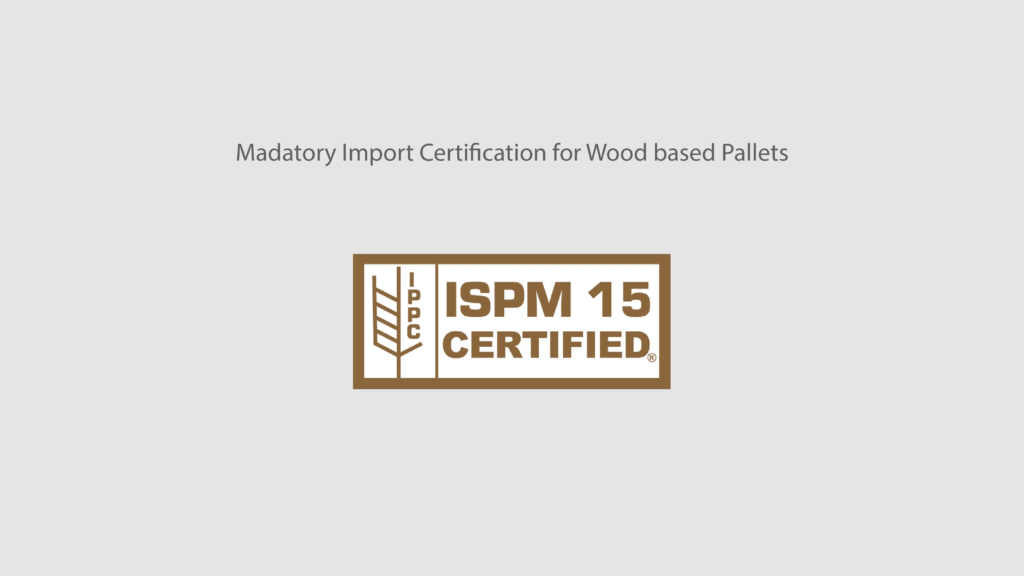
More about IPSM 15: International Standards for Phytosanitary Measures No. 15″ (ISPM-15) was created by the International Plant Protection Convention (IPPC) to address the international shipment of potentially contaminated solid wood materials. Its main purpose is to prevent the spread of insects and disease that could have a negative impact on plants and ecosystems as a result of solid wood packaging used in the international transport of goods. The standard covers vessels, aircraft, vehicles, containers, storage areas, soil, and other materials and objects that can spread and harbour pests.
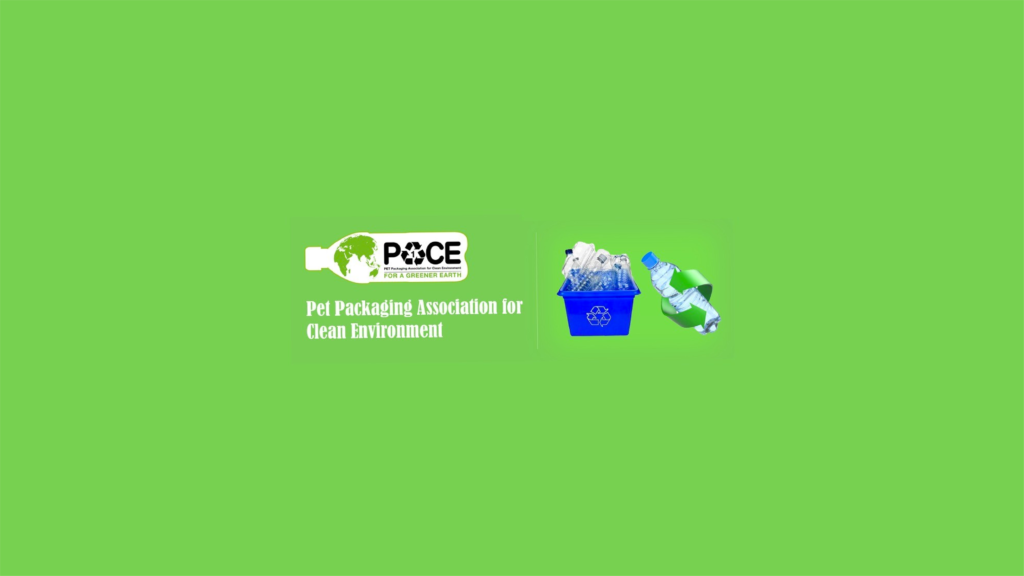
A recent positive development in Indian ecosystem gives a lot of hope, a group of 32 companies including PepsiCo India, Coca-Cola India, Bisleri, Diageo and Reliance Industries have come together to launch a packaging waste management venture and aim to mobilise over Rs 1,000 crore for the purpose. Developed and incubated by the Packaging Association for Clean Environment (PACE), as part of the venture, the participating companies will mobilise and converge assets, resources and investment upwards of Rs 1,000 crore, which will include the existing infrastructure of the member companies and fresh investments. The vision of this venture is to ensure that no recyclable packaging material ends up in landfills by 2025. Read more.
Hoping more such changes in the near future. Through one change, you can achieve everything; a step ahead towards ‘going green’, a higher incentive to reduce cost and owning more brand responsibility towards customers who care. The future of logistic packaging is changing for the better.