With constant change through disruptive technologies, industries are constantly transforming themselves towards a new future. Industrial Logistics is one of them.
The design of the earlier models of logistics and transportation has brought us here where a new leap is expected to bring new scale in our industrial ecosystem. Now, are you ready to go deep with us to know how the logistic packaging can be more eco and freight-friendly.
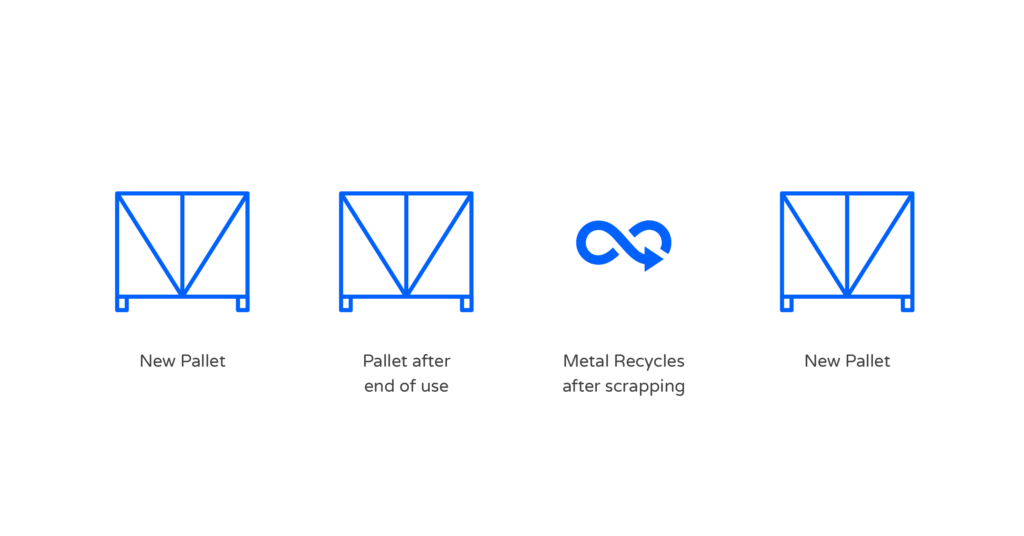
1. Metal packing is recycled at the end of use, saves – environmental footprint compared to pollution by wooden and plastic packing at the end of use
Metal packaging at the end of the supply chain process can be scrapped as a metal commodity and 25% percent value of the original metal packing can be reclaimed.
All brands and manufacturers who use logistics, can minimise their logistic footprint to a minimum by switching to metal engineered packaging. It can be recycled unlike the wooden and plastic packaging which needs another cost for scrapping and recycling, so to avoid it being dumped on to the pollution sites to harm nature and the brand’s reputation switching to metal makes a huge contribution to each business’s green goals.
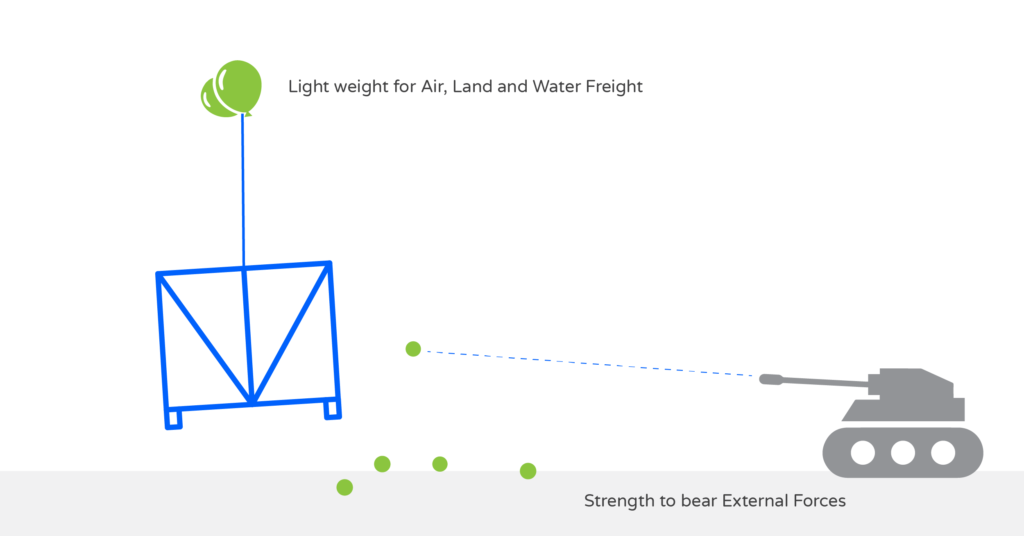
2. Light metal packing do not add to freight cost but adds strength multi-fold
Innovative and highly-engineered metal packaging are designed to be extremely light in weight and highly strong to face any substantial force, when compared to wooden and plastic packaging. Building a metal packing is a process of its own. Understanding its application from the original destination to the end destination and then customising according to the material contained, its size, fragility, price of item, distance to travel, time to transport, mode of transport and so on. Usage of different shapes and grades of metal material is employed to achieve best possible results. Following an innovative design thinking procedure helps standardise the final engineered solution, from understanding the requirements, to designing, testing and sampling till the pilot lot approval is granted, giving value to the users and logistics clients involved.
As a deployed market case: An auto manufacturer gained long-term value from this design innovation. Auto manufacturers want to load more products in a container or a truck by reducing their packing weight for domestic or overseas cross-country shipments. So, one of the leading 2-wheeler manufacturers was able to add 15 additional motor-bikes on their container/truck by shifting from wooden plywood packaging to strong and lightweight metal packaging.

3. Freight Dependency Reduced and Packing ROI Increased after using Stack & Lock Metal Engineered Packing
Damages in the transit are minimized to a large extent using the locking mechanism of stacking metal crates/packings. As an example, the food processing units face a lot of damage inside their retail packaging during transit of products from factory to the warehouses and further to distributors, every single day.
The locking mechanism provides rigidity and stability to the stacks on transit and the rigid frames helped in checking damage to the items inside the packaging. The frames not to mention were engineered customly for the material to be transported which was the main key in saving the items inside from any damage due to force of stacking, irregular movements and jerks in the journey.
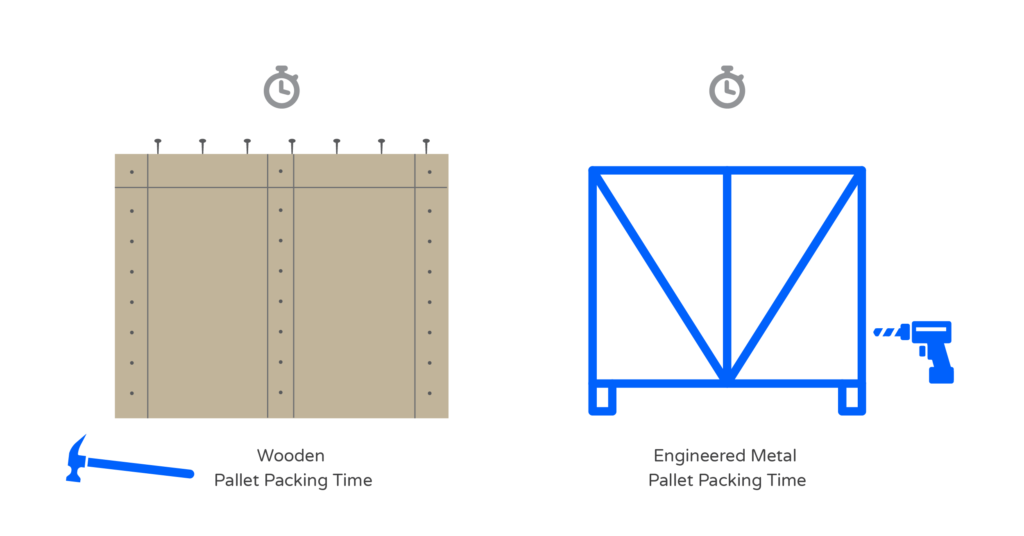
4. Reduced Logistic Packing time in the supply chain process saves freight management time in transit, saves energy and environment compared to manual wooden packing
Metal packings are much safer, faster, easier for logisticians to avoid any kind injury during assembly time, as the complete metal crate is built with utmost care leaving no sharp corners, easier to manage. Assembly of a metal crate is executed using an electric or pneumatic fastening gun. Assembly time of metal packing for fixed no. of SKUs is much faster compared to using a wooden box assembled by iron nails and are mostly done manually by workers and labourers, avoiding dependency on human intervention.
This saves energy, human fatigue, resources, industrial fuel, transit time and in the end the environment.
This is a brief list of benefits using performance based metal engineered logistic packaging. To know more go to our blog www.metalogi.com/blog. Let’s come together and commit ourselves to environmental replenishment and performance logistics.